In industries where metal surfaces are frequently exposed to potential damage, protective films play a crucial role in maintaining their integrity. Whether it is during manufacturing, transportation, or installation, protective films offer a reliable solution to preserve the aesthetic and functional properties of metal. This article explores the benefits, applications, and key considerations when selecting a protective film for metal surfaces.
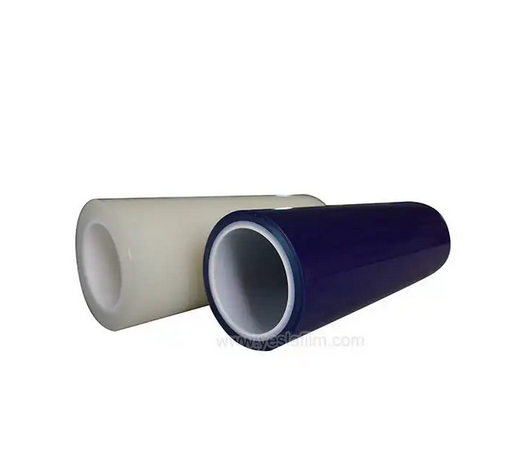
Benefits of Protective Film for Metal
- Surface Protection – Protective films shield metal surfaces from scratches, abrasions, and contaminants such as dust, dirt, and chemicals, ensuring they remain in pristine condition.
- Corrosion Resistance – Some protective films include corrosion-resistant properties that prevent oxidation and environmental degradation, especially for stainless steel and aluminum.
- Ease of Application and Removal – These films are designed for easy application and clean removal, leaving no adhesive residue behind, thus reducing additional cleaning costs.
- Enhanced Aesthetic Appeal – By preventing unwanted marks or stains, protective films maintain the visual appeal of metal surfaces, which is especially critical for architectural and decorative applications.
- Cost Savings – Minimizing surface damage reduces the need for rework and refinishing, ultimately lowering production and maintenance costs.
Applications of Protective Film for Metal
Protective films are widely used across various industries, including:
- Construction and Architecture – Applied to metal panels, stainless steel fixtures, and aluminum facades to prevent damage during transportation and installation.
- Automotive Industry – Used on metal body parts, trims, and panels to protect surfaces during assembly and shipment.
- Manufacturing and Fabrication – Shielding metal sheets, coils, and components from scratches and contaminants during machining and handling.
- Household Appliances – Protecting stainless steel refrigerators, ovens, and dishwashers from fingerprints and scuffs before they reach consumers.
Key Considerations When Choosing a Protective Film
- Adhesive Strength – Selecting the right level of adhesion ensures the film stays in place without causing damage upon removal.
- Material Compatibility – The film should be suitable for the specific type of metal, whether stainless steel, aluminum, or coated metals.
- Environmental Conditions – Factors such as UV exposure, temperature variations, and humidity should be considered to ensure long-term protection.
- Thickness and Durability – Depending on the application, a thicker film may be needed for higher impact resistance.
- Custom Printing and Branding – Some protective films can be customized with logos or instructions, adding an extra layer of utility for manufacturers and suppliers.
Investing in high-quality protective film for metal surfaces is a practical and cost-effective strategy to ensure longevity and maintain the professional look of metal products. By carefully selecting the appropriate film, industries can reduce damage risks, enhance efficiency, and deliver pristine metal components to customers. Whether for construction, automotive, or industrial use, protective films provide a valuable safeguard against everyday wear and tear, ensuring a flawless finish every time.